Choosing a Stepper Motor Power Supply
Some people may consider the stepper motor to be a bit more complex than a standard DC motor. This may be true to a degree, however stepper motors offer many more advantages compared to the DC motors. Some examples of these advantages include; easy control by computer, precise control of rotation, and high torque at low speeds.
Finding a power supply for a stepper motor is fairly easy. In fact, most any standard power supply will do for quick, one-and-done jobs. However, for serious hobbyists and commercial/industrial projects, you might want to put a little more thought into stepper motor power supplies. It’s the best way to optimize performance and maximize the motor’s efficiency, after all.
Here is what we will cover in the factors of choosing stepper motor power supplies.
Table of Contents:
- What is a Stepper Motor?
- Stepper Motor: Practical Applications
- Stepper Motor: Inadvisable Uses
- Why Use Stepper Motor?
- What to Look for in Your Power Supply
- Conclusion
What is a Stepper Motor?
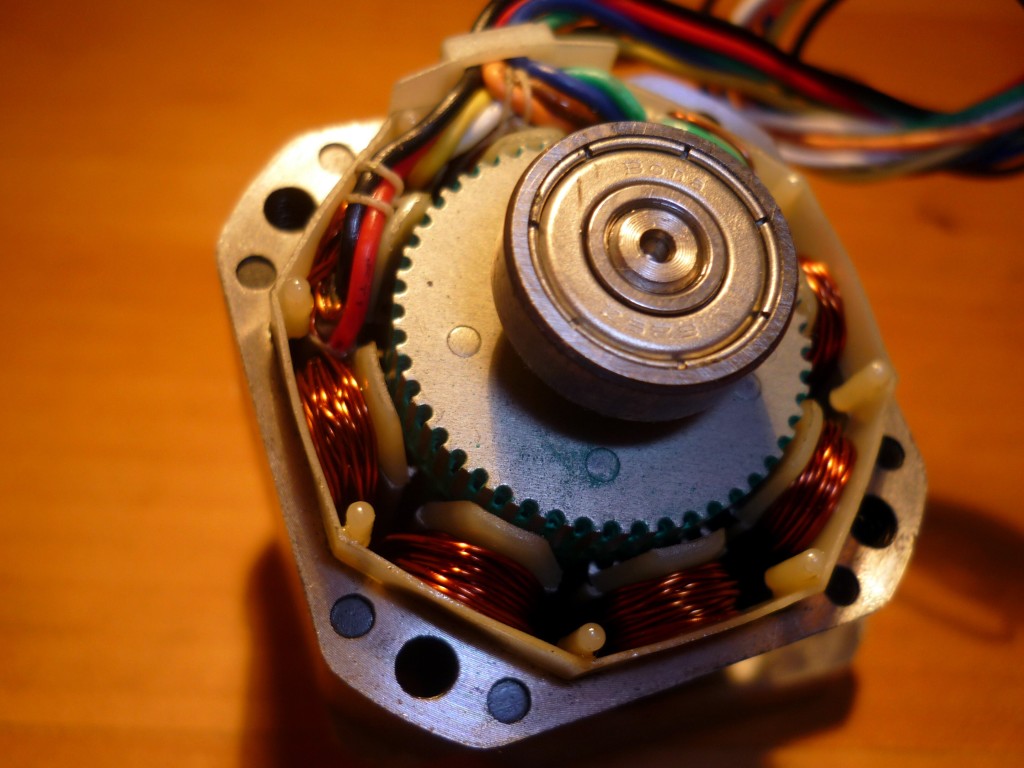
A stepper motor is defined as a “brushless, synchronous electric motor” with multiple coils organized into groups called “phases.” It rotates, one step at a time, by converting digital pulses to energize each phase in a given sequence. These motors are basically DC motors that move in discrete steps dictated by mechanical shaft rotations.
Stepper motors are sent a separate pulse for each step they take, and each step they take is roughly the same size. These pulses cause the motor to rotate at a precise angle (1.8°), consequently controlling the motor’s position without the need for a feedback mechanism.
This is why stepper motors are typically the motor of choice for motion control applications that require high precision.
Stepper Motor: Practical Applications
Stepper motors are used in industrial and commercial settings. In fact, they’re often favored due to their low cost, high reliability, and high torque capabilities at low speed. They’re simple, rugged mechanisms that can function in almost any environment, no matter how rough.
Since stepper motors move in precise, repeatable steps, they’re great for applications that require speed control, low-speed torque, and precise positioning of electronic parts.
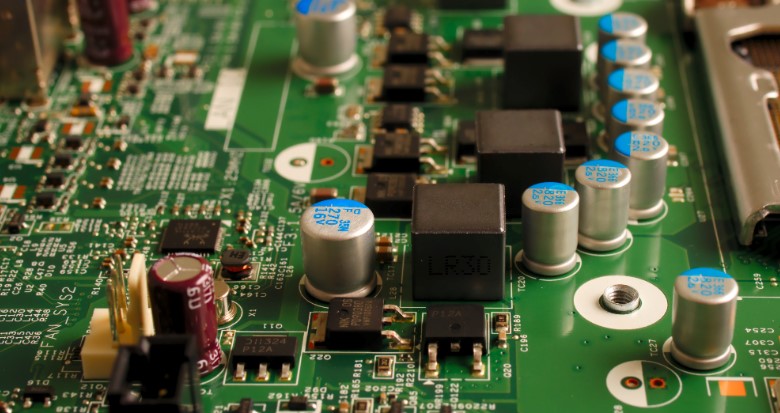
- Positioning. Things like 3D printers, camera platforms, and some disk drives require precise positioning. Stepper motors are perfect for this as they move in precise, repeatable steps.
- Low-Speed Torque. A stepper motor’s maximum torque is always at low speed, which makes them a great choice for applications that need low speed without sacrificing precision. Normal DC motors don’t normally offer the combination of low speed and high precision needed.
- Controlled Speed. Speaking of speed, the precise increments of stepper motors provide excellent control for automation and robotics processes that require rotational speed.
But with these come some limitations that should be taken note of. Just like you wouldn’t use a soldering iron in place of a blowtorch (and vice versa), there are some scenarios where a stepper motor isn’t the best choice.
Stepper Motor: Inadvisable Uses
What stepper motors have in precision and consistency, they lack in efficiency, speed, and feedback.
- Limited High-Speed Torque. As mentioned earlier, stepper motors provide an excellent combination of accuracy and low speeds at max torque. However, this also means that they aren’t ideal for solo high-speed performances.
- Inefficient/Low Efficiency. The current consumption of stepper motors is independent of the load they’re carrying. They tend to run hot on occasion because, unlike DC motors, they draw the most current when they aren’t doing any work.
- Little to no Feedback. One of the biggest drawbacks to using a stepper motor is their lack of feedback. Although they’re great at precision and consistency, most stepper motors do not have integral feedback regarding their position.
Why Use Stepper Motor?
Overall, the advantages of a stepper motor far outweigh the disadvantages—,, especially under the right circumstances. A lot of people consider a stepper motor to be a little more complicated (and fussy) than a standard DC motor and thus aren’t willing to give it a try.
While this, to some extent, may be true, stepper motors shine in practical situations that they were designed for.
Such as the ones we’ve mentioned above, namely 3D printing and hard disk drives. But there are other applications best for stepper motors, too:
- Robotics
- Antennas
- Telescopes
- Clocks/watches
- Traditional printing (paper feed and print wheel)
- Textile machines
- Gaming machines
- Welding equipment
- Factory automation
- Lasers and optics, particularly linear and rotation stages
- Fluid control systems
- Flatbed scanners
- Medical imaging machinery
- Intelligent lighting
- Camera lenses
- CNC machines
- Compact disc drives
It’s important to note that most—if not all—of these applications use a DC power supply to run their stepper motor. This is due to the fact that stepper motors run better and far more efficiently when the voltage is several times higher than their rated voltage.
That being said, knowing what kind of power supply to use for your stepper motor is crucial.
What to Look for in Your Power Supply
When choosing a DC power supply for your stepper motor, you’re going to want to take note of three things: the voltage, the current, and the power supply type. The most complicated factor of these three is usually voltage and current, so we’ll cover those first.
Step 1. Add up the Voltage for Your Stepper Motors Supplies
In order to choose the best power supply for your stepper motor, you’ll need to add up the voltage of the motors. Just like most motors, stepper motors have a rated voltage and current. These numbers will tell you the maximum current you can expect when you hook the motor up to a certain voltage.
For instance, take a typical model with a rated voltage of 2.8 Volts and a current of 1.68 amps. This means that if you hook the stepper motor up to 2.8 volts, it will draw roughly 1.68 amps.
Running it at anything higher than 2.8 will make it draw more current than its max and—in most cases—will cause the motor to heat up excessively. This is why most people won’t hook a stepper motor up to a power source immediately. They’ll instead use a stepper motor driver to regulate the current.
A stepper motor driver ensures that the motor doesn’t attempt to draw more current. This keeps it safe from overheating without compromising the motor’s efficiency.
So first off, determine the number of stepper motors in your system. Make sure they all share the same voltage requirements. Next, add their current rated values.
Say you have four stepper motors. Each motor needs ½ amp (or 0.5 amp) of current.
All in all, your max needed current is 2 amps.
Step 2. Examine the Stepper Motor’s Specifications
Once you’ve added the maximum current you need for your whole system, examine each motor’s specifications to determine the voltage rating. Whatever it is, you’ll need to get a power supply double the rated voltage. So far motors with a rated voltage of 2.8 Volts, you’d need a power supply that runs 5.5 or 6 Volts.
From here, it’s mostly a matter of keeping those numbers in mind and combining it with a bit of research to find the best power supply you can use, like a DC power supply or a variac. Ideally, one that meets both voltage and current requirements without compromising your budget.
Consider Motor Size
One minor factor to consider is motor size with respect to what you expect the motor to do. Larger stepper motors are capable of delivering more power compared to smaller models. Some motors can be smaller than peanuts and still function as expected—just not as powerfully.
Take into consideration the torque ratings of these models. Bigger motors with higher torque and more power will obviously need a DC power supply to match—one that is roughly within its size range.
For instance, NEMA (National Electrical Manufacturers Association) 17 is a size used commonly for 3D printers and the like. Models smaller than NEMA 17—like NEMA 14—can be used in micro-robotic or animatronic applications. And the larger models (like NEMA 57) are often used in CNC machines and industrial applications.
This isn’t true for all motors but sometimes a DC power supply that is roughly the same size of your stepper motor will meet the parameters and requirements of said motor.
Step 3. Browse for Best Offers
Once you know what sort of power supply you’ll need, the final step is to delve into the research. As is the case with most things, it’s probably not the best approach to search “power supplies” and buy the very first item recommended—especially without reading the uses and reviews first, and especially if this is your first time.
Say you’re purchasing electronics kits for adults. You can use a search engine to find a list of recommendations, suppliers, and manufacturers. But then the smartest move would be to carefully review each recommendation, one after the other, to find which one suits your hobbies, expertise, and budget best.
It’s the same with power supplies for stepper motors. There are plenty of blogs, videos, and online stores with a decent selection of power supplies for you to browse. There are also a lot of online forums that you can visit for advice, recommendations, and in-depth discussions with people asking the same thing.
Conclusion
To recap our stepper motor power supplies article here is what we covered:
Table of Contents:
- What is a Stepper Motor?
- Stepper Motor: Practical Applications
- Stepper Motor: Inadvisable Uses
- Why Use Stepper Motor?
- What to Look for in Your Power Supply
We hope this article was informative. Feel free to check out Circuit Specialists’ online store for some pretty good deals.
We have a wide range of fairly-priced stepper motor power supplies that are sure to fulfill all your requirements and parameters.